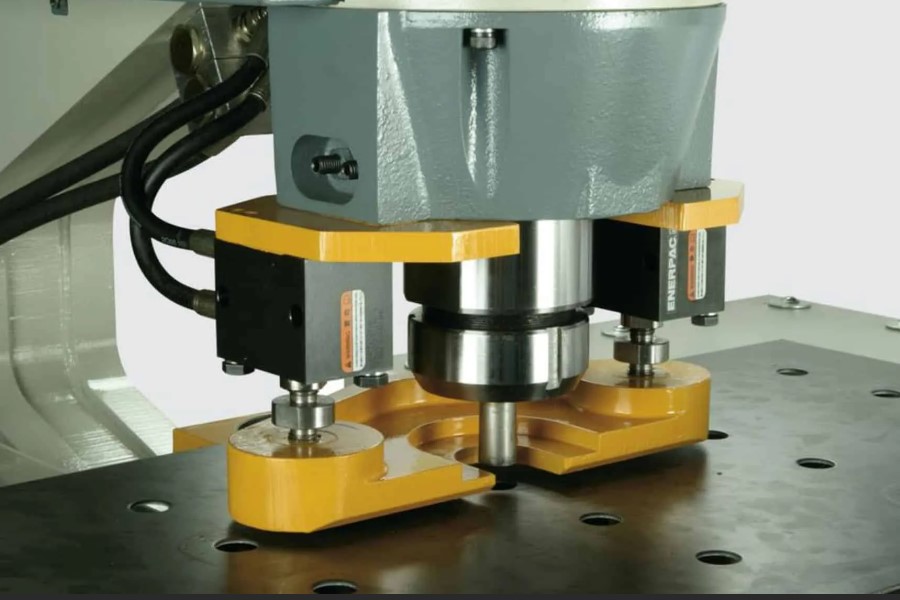
Hydraulic Punching Machine Uses and Advantages
A hydraulic punching machine is used for crushing and forging parts. Compared to the traditional press machines, this type of machine has several advantages. The punching force of this type of machine is invariable, which ensures the accuracy of the punching process. It also simplifies the structure of the turret.
Used For Forging
Hydrostatic presses are a type of forging press used for metalworking processes. They can be purchased in a wide variety of sizes. Sutherland Presses hydraulic forging presses, for example, are available in sizes ranging from 100 tons to 8000 tons. They come with advanced features that make them safe and efficient. They feature enclosed hydraulic systems with steel hoses that eliminate the risk of contamination and spillage. Other features of these presses include automatic lubrication systems, thermal bearing sensors, and electronic monitoring cycles.
Large hydraulic forging presses are used for large-scale forging jobs. This type of press has the capacity to handle large tonnages of metal, such as airplane parts. They can also be used for sheet drawing and transverse pressing.
Used to Crush Materials
Servo-electric hydraulic punching machines perform various processes that require punching materials. These machines are powered by a servo motor and a servo drive. The servo motor delivers constant torque that drives the tube punching movement. High-quality servo motors provide high-speed precision and low noise levels.
Servo-electric machines save energy by using less energy. They consume only about 4.5 kW at high speeds, which is three to four times less than a typical hydraulic machine. They also require less maintenance and are highly reliable.
Efficient
Energy efficiency of the press depends on the size of the flywheel and the main drive motor. Energy savings are relatively small but significant when considered in the context of a machine’s overall performance. An efficient flywheel design can significantly reduce energy demands. On average, an optimum flywheel size can save about 1.1 kJ per cycle of a crankshaft press. This represents approximately three percent of the press’s useful work for one cycle.
Benefits
Programming a hydraulic punching machine can help you get the most out of the machine. Instead of manually punching holes, you can input the coordinates of the hole and let the machine do the rest. This is beneficial because you don’t have to worry about complicated steps. In addition, the machine will automatically calculate how many pieces it needs to make and will operate automatically.
The hydraulic punching machine has three main components: the cylinder that feeds the material, the cylinder that punches the material, and the unloading cylinder. The machine’s three cylinders are linked together by proximity sensors that sense where they are in relation to each other. Once the work piece has been fed, the cylinder drives the origin pin down and the unloading cylinder returns the material to its original position. MEF Industrial Solutions offers it at an excellent price.
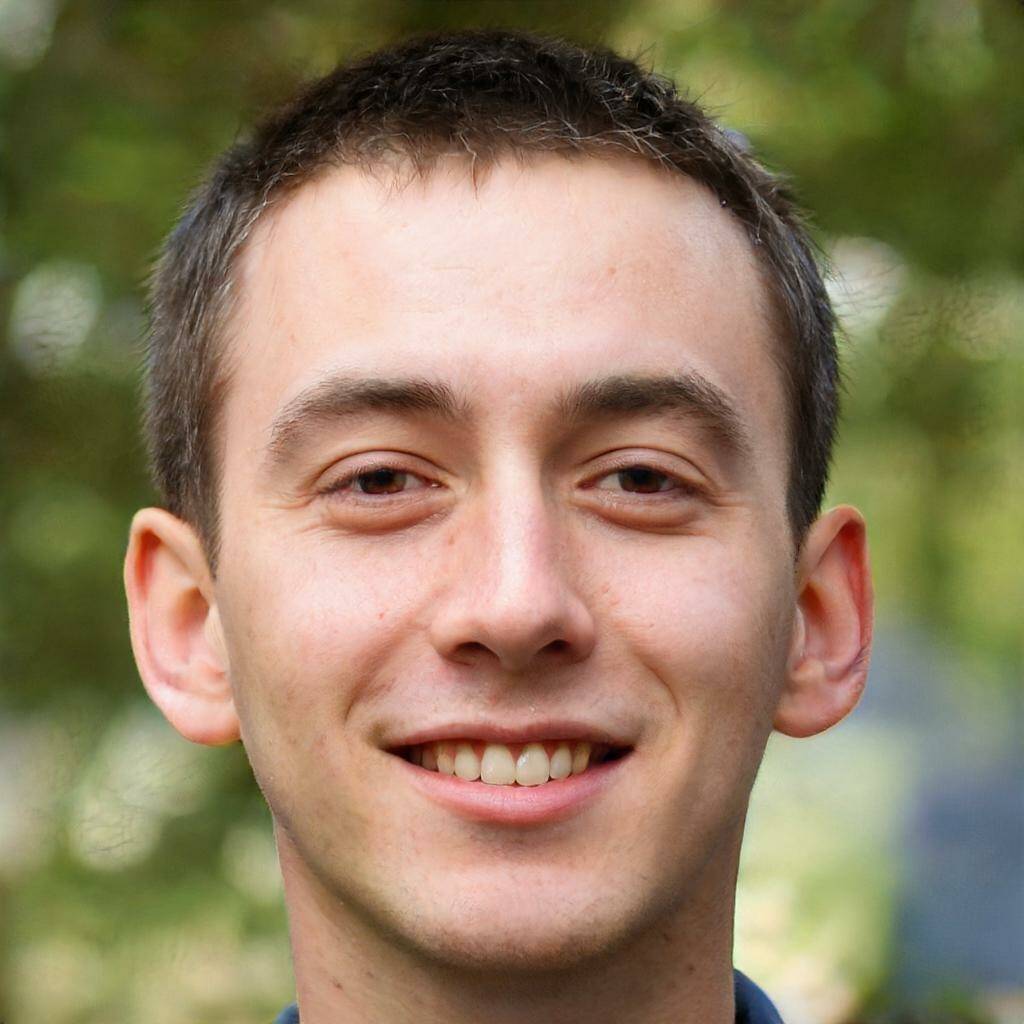
Basketball lover, cooker, music lover, loves to talk about different topics. Let’s chat.